L’impression 3D, au cœur de toutes vos innovations
Vous orienter vers les choix technologiques les plus adaptés
- 01 Ingénierie 3D
- 02 Prototypage rapide
- 03 Outillages
- 04 Production série
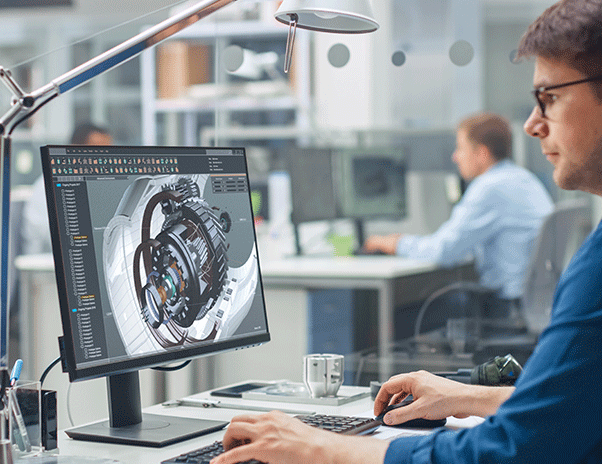
Ingénierie 3D
Depuis sa création en 1991, le Bureau d’Etudes INITIAL est devenue une référence en matière de développement produit. Notre équipe d’ingénieurs et projeteurs dispose d’une grande expertise en conception de produits alliée à une démarche innovante.
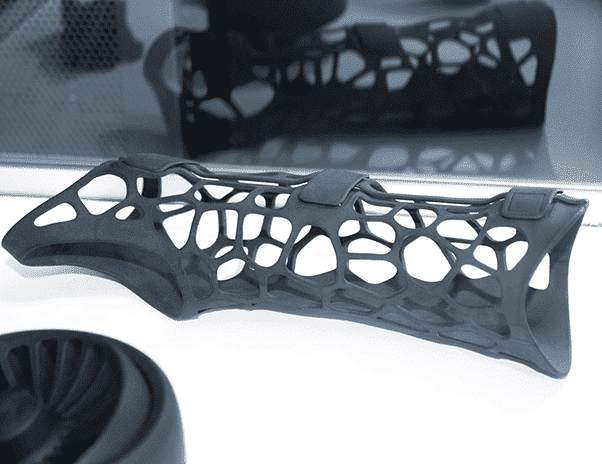
Prototypage rapide
De la bonne intégration de vos besoins à la proposition de solutions adaptées et originales, INITIAL se démarque en vous proposant des solutions innovantes de prototypage rapide plastique et métal ainsi qu’une capacité de production unique.
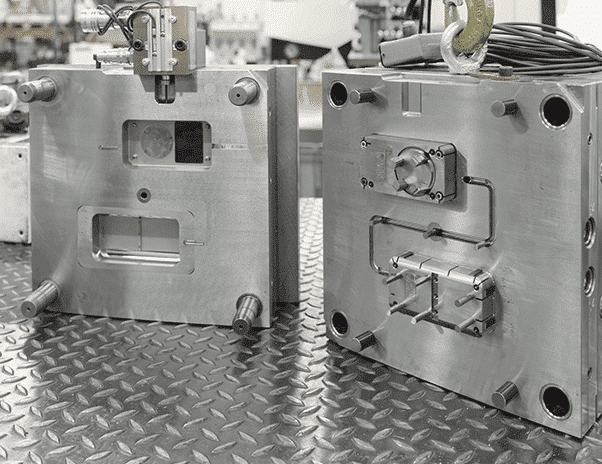
Outillages
Nous réalisation la conception de vos moules au sein de notre bureau d’études dédié. Grâce à nos différentes technologies d’outillages, nous vous proposons des solutions adaptées à la production de vos pièces prototypes bonne matière ou vie série.
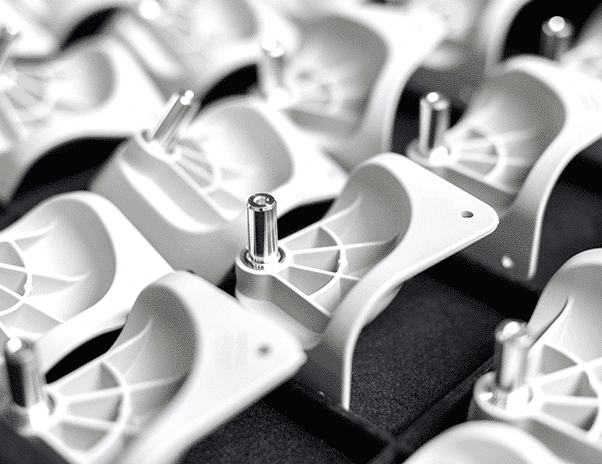
Production série
Les thermoplastiques techniques sont transformés dans les conditions classiques de production de pièces séries et un contrôle qualité adapté à votre demande est mis en œuvre. La souplesse de notre structure permet des productions courtes et des délais réduits.
Des pôles exclusifs dédiés à vos innovations
Vos défis, nos productions
À chaque challenge, bénéficiez de nos solutions technologiques et de nos capacités de service et d’accompagnement pour répondre à vos applications les plus exigeantes. Découvrez nos dernières réalisations.
Toutes nos productions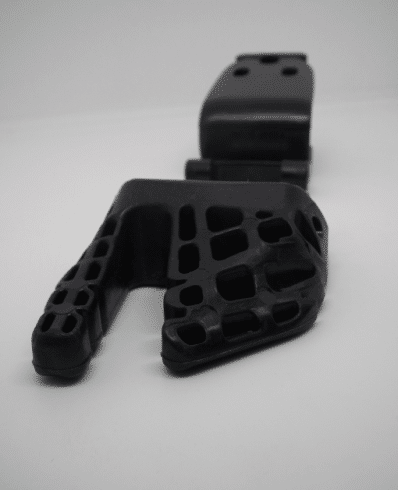
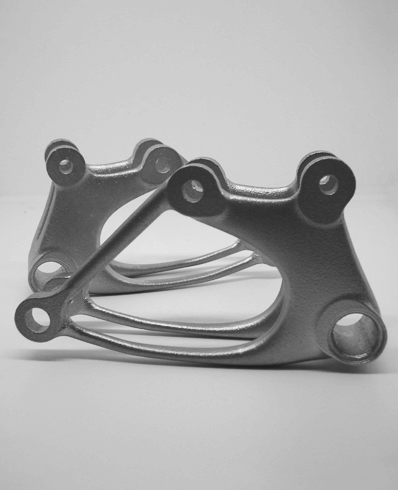
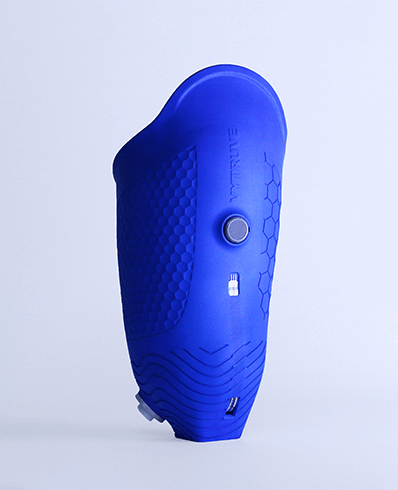
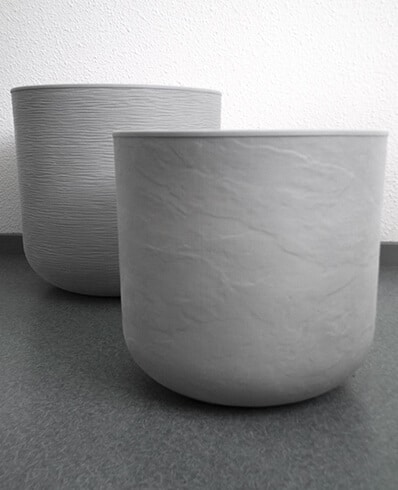
Vous avez un projet ?
Notre équipe de professionnels vous conseille et
vous guide vers les meilleurs choix pour tous vos projets.
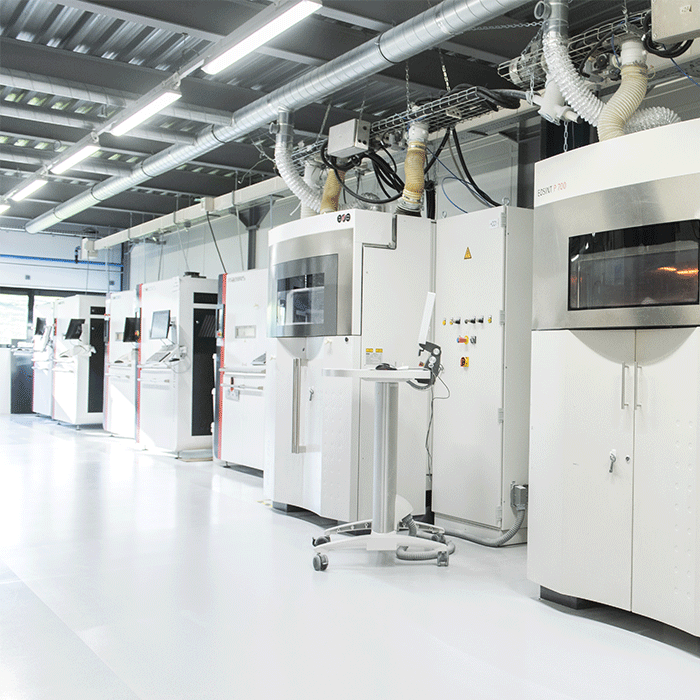
L’industriel agile, producteur de vos conceptions 3D
Bienvenue dans une entreprise où expertise, innovation et satisfaction client sont les maîtres-mots !
Notre volonté : vous offrir une solution globale clé en mains en vous apportant expertise et compétitivité.
C’est le défi que relèvent nos équipes au quotidien. Nos collaborateurs formés aux dernières technologies mettent en commun leurs compétences à votre service.
Plus de flexibilité, plus de réactivité !
Notre actualité
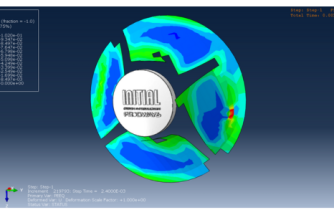
Découvrez ABAQUS : Notre nouvel atout en simulation numérique
Initial vient d’intégrer le logiciel ABAQUS® de l'éditeur 3DS à son offre de services numériques. ABAQUS® se positionne comme une référence dans le domaine de la simulation numérique par éléments finis, grâce à ses performances et sa fiabilité.
Lire plus
Testez et caractérisez l’impression 3D métal
Testez et caractérisez l'impression 3D métal grâce à des "éprouvettes"
Lire plus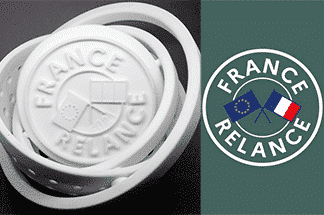
France relance industrie
Une subvention obtenue pour le programme de R&D « Futur3D », dans le cadre du Plan de Relance Industrie.
Lire plus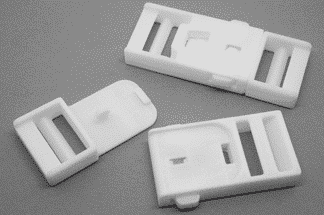
Le PA11, une nouvelle matière 100% biosourcée
Polymère 100% biosourcé et dérivé de l’huile de ricin vient enrichir notre offre d'impression 3D plastique.
Lire plus