Short run 3D printing for Morel
First collaboration
Short run 3D printingThe Jura-based eyewear manufacturer MOREL has been continuously reinventing and innovating since 1880, creating innovative, stylish and extremely comfortable frames.
That’s why when it came to producing its LIGHTEC glasses, it naturally turned to INITIAL, the French leader in 3D printing based in the Upper Savoy region.
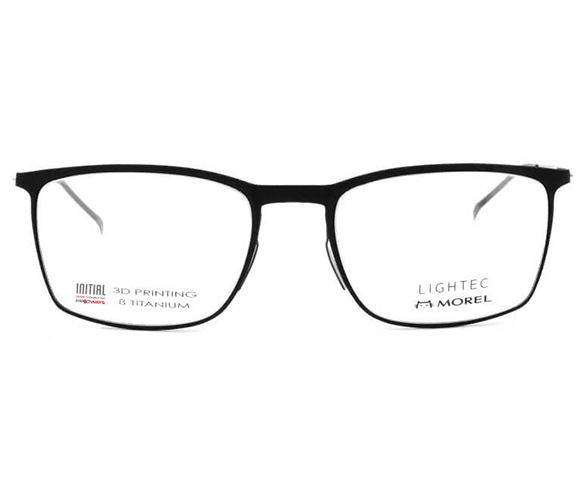
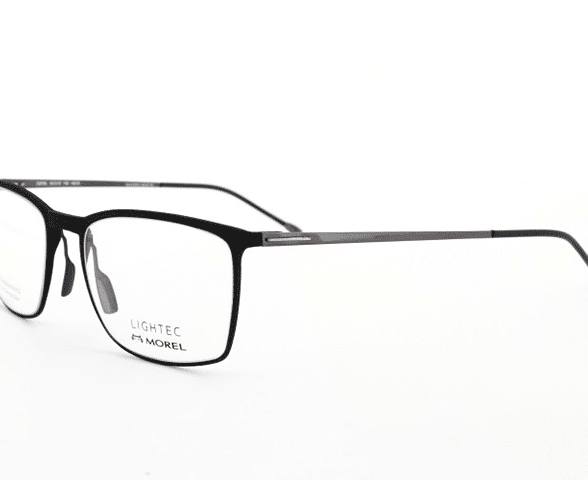
A design-based strategy
With its short run 3D printing expertise, INITIAL offered MOREL a new dimension for producing its glasses.
Production technology that enables the frames to be reproduced exactly as intended by the designers, free of technical constraints.
Design freedom is one of the core values of both these French companies, driven by a constant search for innovation.
The frames come in endless combinations in terms of size and can be highly customised.
Agile custom-made mass production
This technology, which is also known as Additive Manufacturing, appealed to MOREL thanks to its freedom of design and production.
The polyamide fronts are produced by 3D printing using SLS® powder sintering.
The material is flexible, extremely lightweight and virtually unbreakable.
3D printing enables a raw product to be obtained, with a pile that is reminiscent of velvet.
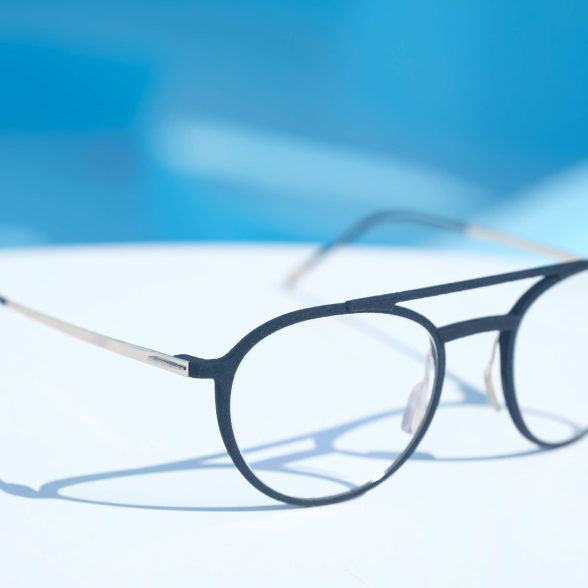
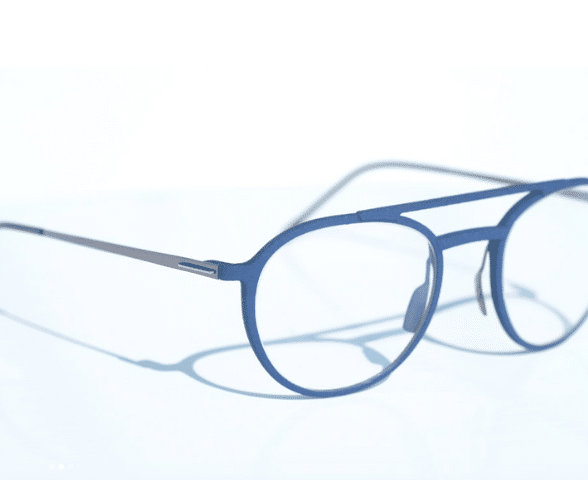
A marvel of technology and comfort
- The fronts are combined with beta titanium arms, which are both lightweight and strong.
- These 3D printed glasses are as light as a feather, weighing just 10 g.
- MOREL embellishes its frames using a palette of deep colours: the dye penetrates deep into the material for a bright and intense result.
- The glossy arms contrast with the eye-catching colours of the polyamide front.
A high-tech and extremely refined product.
The entire piece, including the lens and frame, is assembled by MOREL.
Unprecedented mass production
The launch of this manufacturing process represents a step forward in Initial’s strategy, leading the way in the additive manufacturing of mass-produced plastic parts:
MOREL is aiming to become the leading eyewear manufacturer and has drawn on the potential of additive manufacturing by working with INITIAL, the French leader in this field.
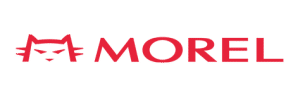
“The entire INITIAL team are delighted with this collaboration with MOREL, a company that fully understands how to make the most of the benefits of this technology. An extremely positive and high-quality result.”