Mechanical, thermal and fluid simulation
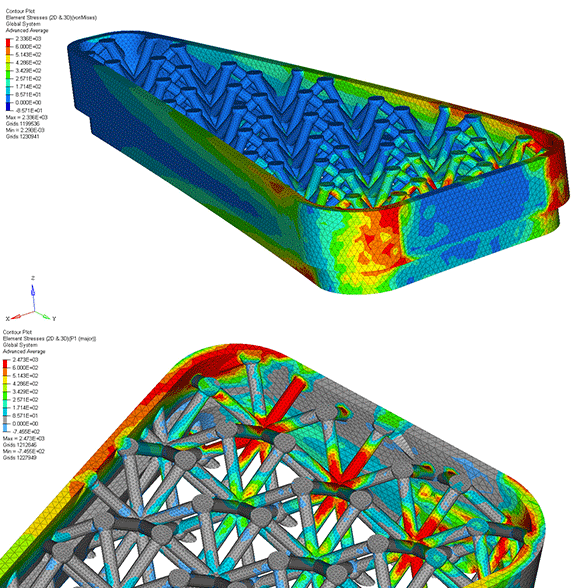
Digital simulation
Mechanical simulation
INITIAL can help you generate an authentic representation of how your parts and products behave.The aim of mechanical simulation is to predict the behaviour of an assembly or component in response to external mechanical stresses such as pressure, forces, pre-stresses, etc.
When is mechanical simulation appropriate?
- To dimension a geometric form.
- To optimise the geometry of a part for greater strength and improved performance.
- To select a production material based on the requirements of the specifications.
- To examine the transfer of manufacturing technology.
Thermal simulation
Thermal simulation enables us to predict heat transfers within a part and/or with the external environment.
Measure heat balances to analyse the temperature field and heat flows in a steady or transient state.
Improve heat dissipation by extracting heat calories:
- Optimise the thermal behaviour of a tool by combining thermal & fluid effects within the same simulation.
- Reduce the cooling time for parts or dedicated systems.
- Maximise heat extraction via conduction and/or natural or forced convection phenomena.
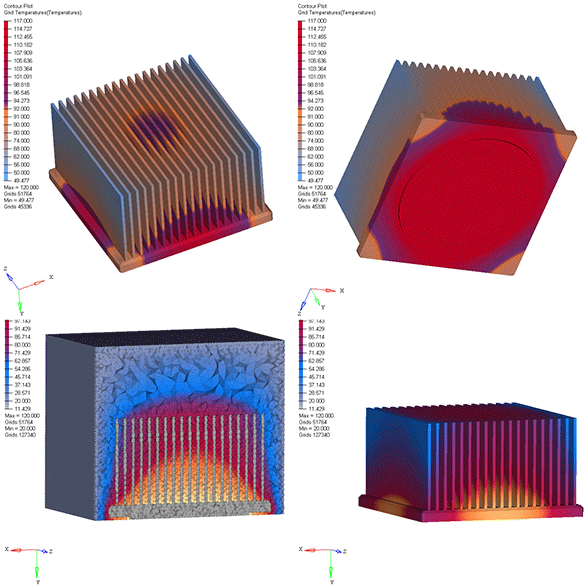
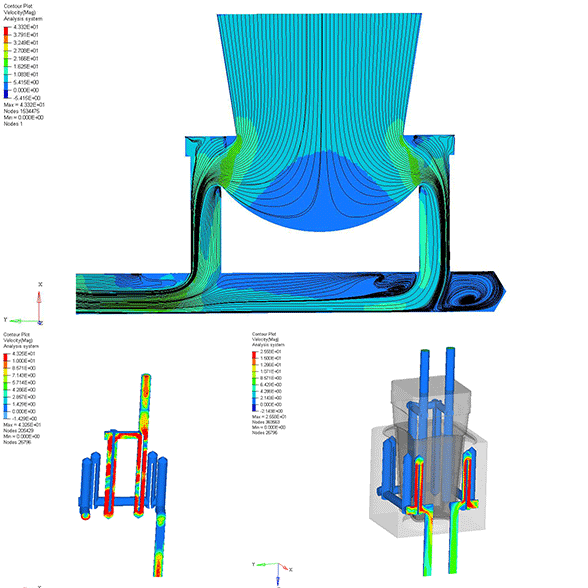
Computational Fluid Dynamics (CFD)
Fluid simulation
Fluid flow simulations (Computational Fluid Dynamics or CFD) are based on algorithms enabling analysis of the flow behaviour of air, water, or any other fluid.
Fluid simulation enables:
- assessment of pressure losses in ducts,
- visualisation of velocity fields and observation of flow pressure fields.
- Improving the production cycle of a part is directly related to the part cooling time in the injection mould.
Hence the possibility of combining thermal & fluid effects within the same simulation.
This process is commonly known as conformal cooling.
This type of simulation is particularly suited to the analysis of electronic component heating where cooling and insulation are required: heat sink, furnace, etc.
From analysis to results
Our approach to digital simulation: a tried and tested methodology- In accordance with the conditions of use of your product, we define the stress points to which it is subjected and draw up the appropriate load cases.
Such changes may be applied to parts from an assembly or applied to the full assembly (to manage mechanical switches or thermal and fluid interfaces). - Using the 3D files of the part or assembly (in .step, .iges, or native file format), we complete the simulation to extract pertinent data.
- Following the simulation, we can provide the colour maps that translate the part behaviour (constraint fields, temperature fields, or pressure and speed as part of a fluid simulation).
- If the digital simulation approach reveals that the part is incompatible with the requirements of the specifications, we will optimise the part geometry.
We deliver the 3D file (.step or native) for the optimised part, which may incorporate production constraints.
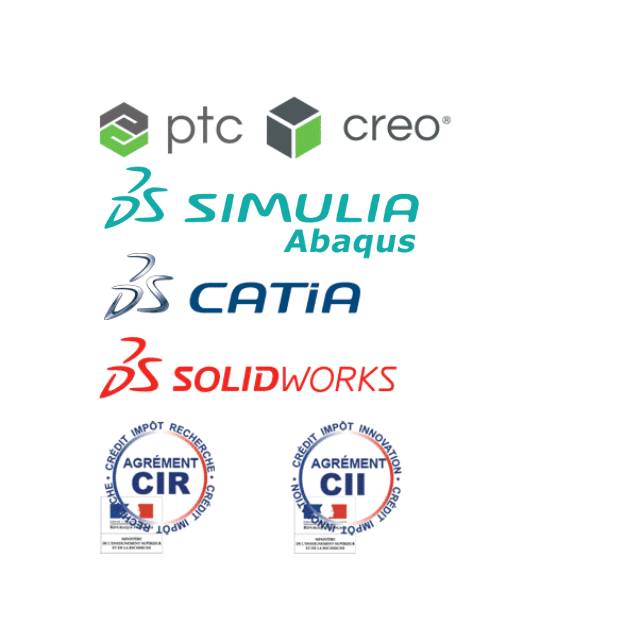
Technical expertise
Our dedicated simulation unit
INITIAL uses ABAQUS® to deliver all its simulation services.The ABAQUS® environment together with our 3D model generated using the Creo® software offers generous flexibility to optimise part geometries.
- Know-how in plastic materials related to our specialist activity.
- Advice in selecting appropriate materials.
- We incorporate the production constraints of the part in the dimensioning stage or during optimisation.
- Expertise in the additive manufacturing sector.
DELIVERABLES
- Detailed summary report with interpretation of results.
- 3D model of optimised part.
- Recommendations for choice of materials.